Warning: strpos() expects parameter 1 to be string, array given in /home/site/wwwroot/wp-content/themes/twentynineteen-child/functions.php on line 163
Dentro del diseño de transmisiones rígidas se resaltan elementos que transmiten potencia y movimiento, en los que una leva transmite una secuencia de movimientos de un árbol de transmisión a un seguidor que realizará un movimiento alternativo, mientras que los engranajes transmiten potencia, es decir, momento torsor y velocidad angular, con un movimiento continuo entre dos árboles de transmisión, de acuerdo con una relación de transmisión i = ω2/ω1.
Ambos elementos de máquinas se comportan como un mecanismo de cuatro barras. En el caso de los engranajes se define un axoide como el lugar geométrico de los ejes instantáneos de rotación y deslizamiento en el movimiento de un segundo cuerpo que gira alrededor del eje X, respecto del primer cuerpo que gira alrededor del eje X. Dependiendo de la posición de los ejes que forman el axoide los engranajes se pueden clasificar en: cilíndricos (paralelos), cónicos (intersecan) e hiperbólicos (se cruzan).
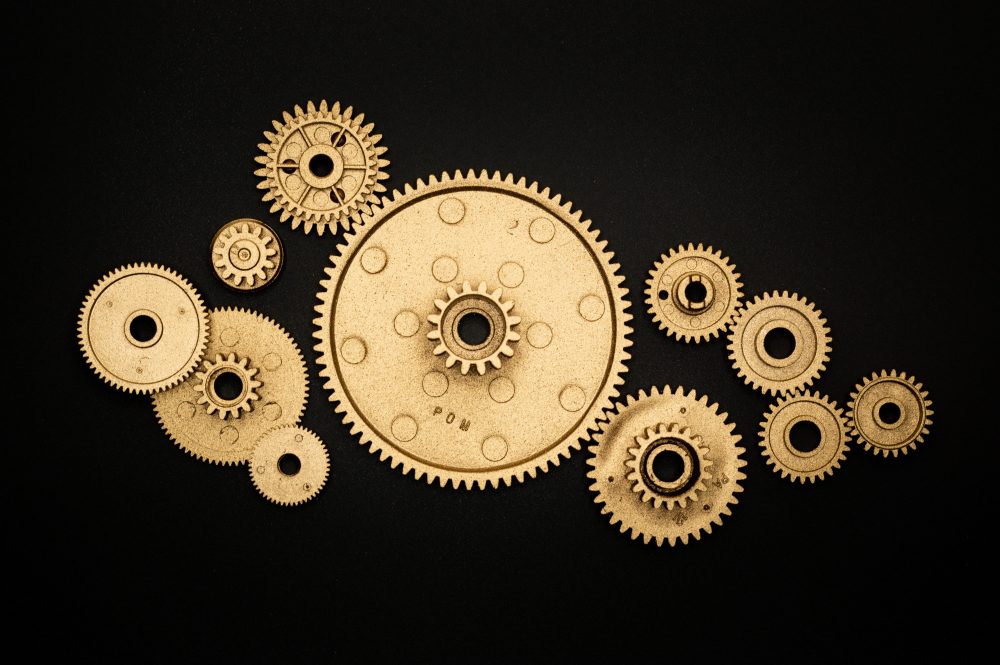
Levas
Los sistemas leva – seguidor se clasifican de varias maneras, por el tipo de movimiento del seguidor en traslación y rotación, por el tipo de leva en radial, cilíndrica y tridimensional; por el tipo de cierre en forma o fuerza, por el tipo de seguidor en curvo, plano y rodante; por el tipo de restricciones de movimiento en posición crítica extrema CEM y movimiento de trayectoria crítica CPM, y por el tipo de programa de movimiento en subida – bajada, subida – bajada – meseta y subida – meseta – bajada – meseta.
Para asegurar el programa de movimiento se utilizan diagramas s-v-a-j (posición – velocidad – aceleración – sobre aceleración) que se obtienen desenrollando la leva de manera que se ve una función linealizada. En esta función se debe asegurar que no haya cambios bruscos de velocidad, por lo que se debe cumplir la Ley fundamental del diseño de levas. Esto indica que “la función de leva debe ser continua en la primera y segunda derivada de desplazamiento a través de todo el intervalo”.
Acompañada de un corolario que indica que “la tercera derivada, función sobre aceleración, debe ser finita a través de todo el intervalo”. Las funciones más habituales usadas en el diseño de levas son la de movimiento armónico simple, de la forma s = h/2[1-cos(πθ/β)]; desplazamiento cicloidal, de la forma s = h[θ/β-1/(2π)sen(2πθ/β)]; y funciones polinomiales de grado 5 o superior, según las restricciones de movimiento que se requieran. Partiendo de estas ecuaciones se pueden obtener la velocidad (v), la aceleración (a) y la sobre aceleración (j) derivando la función inicial. Además, multiplicando el resultado por la velocidad angular de la leva de la manera S=sω0,V=vω1, A=aω2 y J=jω3.
Engranajes rectos
Los engranajes rectos se caracterizan por tener dientes paralelos al eje de rotación y se emplean para transmitir movimiento de un árbol de transmisión a otro árbol paralelo. Para el diseño de engranajes se utiliza una terminología específica, en primer lugar, la circunferencia primitiva o circunferencia de paso. Se define como una circunferencia teórica lisa que sustituye a una rueda dentada, es decir una pareja de engranajes equivale a dos ruedas lisas con diámetro primitivo. Estas son tangentes entre ellas y transmiten momento torsor debido al coeficiente de rozamiento entre ambas.
Sobre estas ruedas se puede calcular la relación de transmisión i. Sin embargo, el coeficiente de rozamiento tiene un valor limitado, por lo que existe una limitación de momento torsor. Esto para aumentar este momento se tallan dientes en las ruedas primitivas. El engrane entre los dientes requiere de la Ley general del engrane, que dice; “en el contacto de dos perfiles, para que la relación de transmisión si sea constante se debe cumplir que la normal a los perfiles. Esto en el punto de contacto debe pasar siempre por un punto fijo de la línea de centros, este punto se denomina ‘punto primitivo’”.
La línea de engrane, o línea de presión, entre dos dientes es una recta tangente a ambas circunferencias base que pasa por el punto primitivo, el ángulo de esta línea con una recta tangente a ambas circunferencias primitivas se denomina ángulo de presión φ, que esta normalizado a 20º y, en menor medida a 14,5º, 22,5º y 25º.
Reglamentación
Se debe señalar que la Norma DIN 3967:1978-08 Sistemas de ajustes de engranajes; retroceso, espesores de dientes y tolerancias de espesores de dientes; principios, indica los espesores finales de dientes para diferentes aplicaciones (maquinaria pesadas, automóviles, maquinaria agrícola, …), y el retroceso, o backlash, teórico y de funcionamiento, que es la diferencia entre el ancho del hueco y el espesor del diente, considerando la tolerancia de la medida, los coeficientes de dilatación térmica de los materiales, la tolerancia de la distancia entre centros, los errores de paralelismo de los ejes, de posición y forma de los dientes, y la elasticidad del material.

A estos factores se les puede añadir el adendo a, o cabeza, que es la distancia radial entre la circunferencia primitiva y la circunferencia exterior del engranaje, por defecto, su valor coincide con el módulo m, el dedendo d o raíz, que es la distancia radial entre la circunferencia primitiva y la circunferencia interior del engranaje, por defecto, su valor es 1,25 veces el módulo m.
La altura del diente, entendida como la suma del adendo y del dedendo, y el juego c, definida como la distancia radial entre la circunferencia interior de un engranaje y la circunferencia exterior de su pareja, por defecto su valor es 0,25 veces el módulo. Se define el deslizamiento específico ξ como la relación entre la velocidad de deslizamiento y la velocidad en dirección tangente al diente ξ=vd/vt e indica el comportamiento al desgaste de los engranajes.
Engranajes cónicos
Los engranes cónicos, denominados así por presentar dientes formados en superficies cónicas, se emplean sobre todo para transmitir movimiento entre ejes que se intersecan. Estos engranajes pueden tener los dientes rectos, en espiral, que se forman de manera que el diente describa un arco circular, y los engranes hipoides que son muy similares a los engranes en espiral, excepto por el hecho de que los ejes están desplazados y no se intersecan. Por lo general estos engranes forman un ángulo de ejes de 90°, pero pueden formar casi cualquier ángulo.
El paso diametral de los engranes cónicos se mide en el extremo mayor del diente; tanto el paso circular como el diámetro primitivo se calculan de la misma manera que en los engranes rectos. Los ángulos de paso se definen por los conos de paso, unidos en el ápice y que se relacionan con los números de dientes según las relaciones tanγ=NP/NG; tanΓ=NG/ NP; donde los subíndices P y G se refieren al piñón, o rueda más pequeña, y a la corona, o rueda mayor, respectivamente, y donde γ y Γ son los ángulos de paso del piñón y de la corona.
Cuando se proyectan los dientes en el cono posterior, esta proyección es la misma que en un engrane recto con un radio igual a la distancia al cono posterior rb. Esto se conoce como aproximación de Tredgold. El número de dientes en dicho engrane hipotético es N’=2πrb /p; donde N’ es el número virtual de dientes y p es el paso circular medido en el extremo mayor de los dientes.
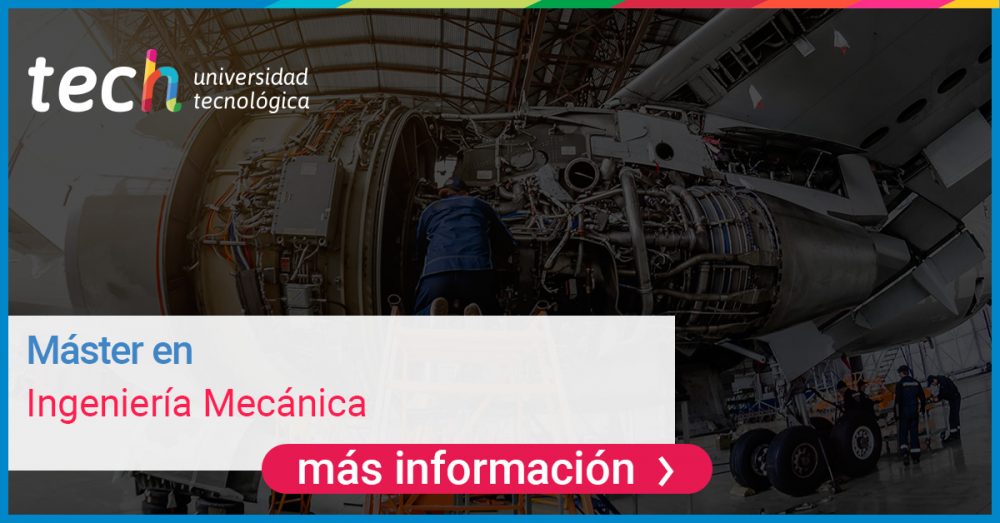
Diseño de maquinaria
El ingeniero cuenta con una gran amplitud de campos en donde puede aplicar sus conocimientos. Esta profesión se ha constituido como una de las más importantes en el desarrollo del progreso en el ser humano y la industria. Por ello, el mismo debe contar con plena seguridad y conocimiento, además de una amplia experiencia con respecto a su labor.
TECH Universidad Tecnológica oferta en la actualidad un amplio portafolio educativo enfocado en el proceso de crecimiento del profesional. En el caso de su Facultad de Ingeniería, destacan posgrados tales como el Máster en Ingeniería Naval y Oceánica y el Máster en Industria 4.0 y Transformación Digital. Sin embargo, para aquellos profesionales que buscan dominar el campo del diseño de maquinaria, no cabe duda que su mejor decisión será optar por el Máster en Ingeniería Mecánica.