El objetivo de las tareas de mantenimiento es reducir las incidencias a lo largo del proceso productivo, con el objeto de mejorar la disponibilidad de la máquina, evitando roturas u optimizando el rendimiento de los equipos o componentes industriales, evitando pérdidas de velocidad. Una buena labor en las operaciones de mantenimiento puede ahorrarle al director de operaciones muchos quebraderos de cabeza, ya que pueden perjudicar tanto a los tiempos, las cantidades y a las calidades del producto. No siendo solo importante el control en el mantenimiento de los equipos, sino también en las instalaciones para conseguir un buen funcionamiento y conservación general del sistema.
Es por ello, que el mantenimiento industrial tiene unos objetivos muy claros para desarrollarse:
- Evitar, reducir y reparar, si fuera necesarios, fallos en los equipos.
- Evitar fallos de gravedad.
- Evitar paros de máquinas.
- Evitar accidentes, mejorando la seguridad de las personas.
- Conservar de forma segura los bienes.
- Prolongar la vida de los bienes.
El coste que implica la gestión del mantenimiento también debe ser considerada por el director de operaciones, ya que debe ser tal que cumplan los objetivos de mantenimiento siempre que no supere el coste del reemplazo por una máquina nueva. Entre estos costes se considerarían: mano de obra, coste de materiales, repuestos, nuevas piezas, energía, combustibles, pérdidas por la no producción.
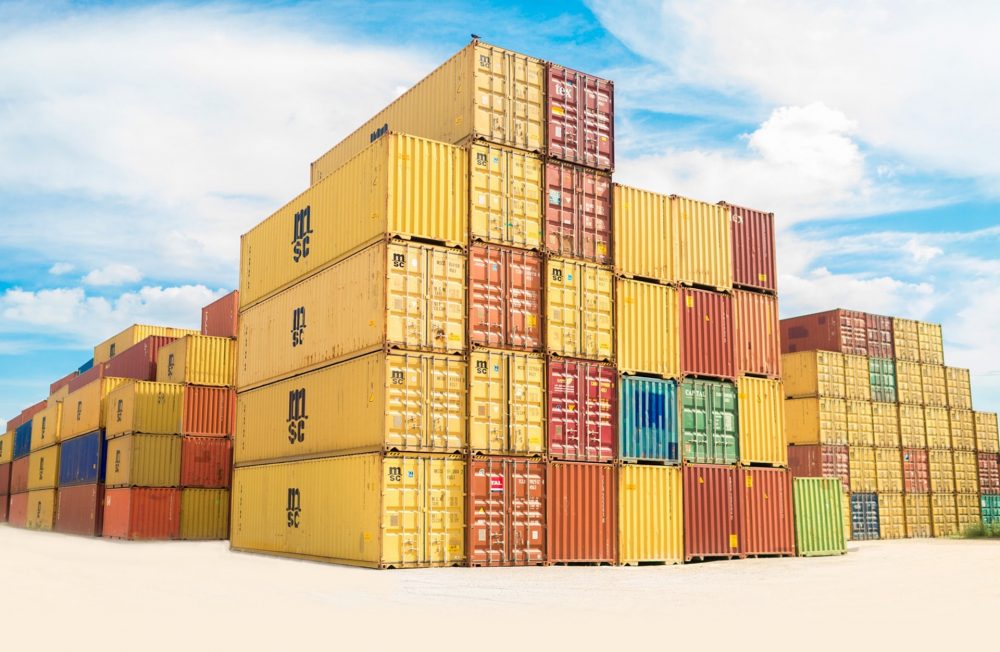
Tipos de mantenimiento
Existen varios sistemas o conjunto de técnicas para realizar el mantenimiento de las instalaciones. En dependencia de su tipo de actuación se realizará la siguiente clasificación:
Mantenimiento correctivo
Es el conjunto de tareas de mantenimiento que se realiza una vez los defectos se han presentado en los equipos. Suelen ser comunicados al departamento de mantenimiento por los propios operarios de las máquinas. Este tipo de sistema puede ser:
• No planificado: Denominado mantenimiento de emergencia, ya que es un fallo imprevisto que debe resolverse rápido porque puede ocasionar problemas
adicionales de seguridad, contaminación, entre otros. Puede ser aplicable en sistemas bastante complejos en los que es imposible predecir el fallo o en procesos que es imposible parar la línea, ya que es más costoso hacer esta tarea que la pérdida de los costes de material no producido.
• Planificado: Debido a la experiencia, se sabe cómo afrontar el fallo pudiendo reservar los recursos para cuando suceda tanto en personal como repuestos o
técnicas para poder resolverlo. El problema de este sistema es la inversión en
repuestos que se deben de tener para poder resolverlo en el menor tiempo posible.
Mantenimiento preventivo
Es el conjunto de tareas de mantenimiento que tienen como misión prevenir los fallos y mantener un nivel de servicio determinado en los equipos. Son actividades programadas como inspecciones, pruebas, intervenciones en puntos vulnerables del sistema, etc. La planificación que se realiza para este tipo de
mantenimiento es la definición de partes o elementos a mantener, establecimiento de la vida útil de los elementos, determinación de los trabajos a realizar y establecer los periodos de actuación de las reparaciones.
Este tipo de mantenimiento tiene un carácter sistemático, se repara antes de que ocurra cualquier fallo o puedan existir síntomas de problemas. Es por ello, que tiene ciertos inconvenientes como:
• Cambios innecesarios por un establecimiento de la vida útil del elemento más corta de lo que podría ser. Aprovechando el paro se realiza mantenimiento del sistema completo, como otras piezas menores en buen estado.
• Problemas en los ajustes al inicio de la producción que puede generar diferencias en la estabilidad, seguridad o regularidad de la marcha. Incremento de los costes en inventarios en las piezas de reposición.
• Incremento del coste de la mano de obra necesaria para la realización de acciones específicas.
Mantenimiento predictivo
Es el conjunto de tareas de mantenimiento que persiguen conocer e informar permanentemente a través de la monitorización del estado y la operatividad
de las instalaciones. Teniendo el conocimiento de los valores de determinadas variables representativas de tal estado y operatividad que permiten una intervención correctora inmediata ante la detección de algún síntoma de fallo.
Este método se basa en la premisa de que los fallos se producen después de unos indicios evidentes a simple vista o a través de su monitorización, por lo que es necesario identificar las variables fisicoquímicas cuya variación sea indicativa de problemas que puedan aparecer en el equipo. Es el tipo de mantenimiento más tecnológico y avanzado, ya que requiere de medios analíticos y técnicos avanzados mediante sistemas de equipos sofisticados.
La ventaja de este sistema permite tener un registro histórico de los fallos, que se pueden analizar para programar futuras reparaciones programando las
paradas de mantenimiento evitando intervenciones innecesarias de la mano de obra. Otra de las ventajas es que los costes de monitorización son menores a
la mano de obra de mantenimiento y de la indisponibilidad que genera la máquina.
Algunos de los métodos de mantenimiento predictivo son: control en marcha (inspección visual, acústica y al tacto de los componentes accesibles, temperatura, lubricante, pérdidas, vibraciones, ruidos o corrosión),
control en parada (inspección visual, acústica y al tacto de las partes en movimiento o inaccesibles, fisuras, fugas, vibraciones o corrosión) y control
de condición de aplicación general (lubricantes, temperatura o vibraciones y ruidos).
Un ciclo básico del control del mantenimiento tendrá ciertas entradas a la planta y una serie de salidas con objetivos, pero hay otro flujo que se debe tener en cuenta y es por donde se muestran las salidas y se analizan las muestras, aplicándose medidas correctivas si son necesarias.
Este ciclo representado por un ciclo de control de mantenimiento tendría las siguientes características:
- Entrada a planta: instalación que recibe la información.
- Salida de planta: objetivo de disponibilidad y nivel de calidad.
- Muestra de las salidas son: órdenes de trabajo, archivo histórico, condición del equipo e informes de costes y calidad.
- Análisis de las muestras suponen: el análisis de las tendencias, medidas de desempeño y tendencia de tiempo muerto.
- Acciones correctivas: revisión de las políticas de mantenimiento, programación del mantenimiento y especificación de los trabajos.
Establecidos los flujos de control de mantenimiento, se pueden diseñar distintos programas de mantenimiento con el objetivo de mejorar la disponibilidad en planta, reducir costes, mejorar la confiabilidad del equipo y controlar la calidad del producto.
Sistema de órdenes de trabajo de mantenimiento (ODT)
En el sistema de órdenes de trabajo se detallarán las operaciones de los trabajos de mantenimiento, conteniendo información y datos que posteriormente, serán analizados para la ejecución de trabajos y comprobar la calidad, costes, tiempos, la fiabilidad y disponibilidad.
El departamento de mantenimiento debe ser el responsable de estas tareas de administración de las órdenes con la supervisión del director de operaciones. En estas tareas administrativas se debe incluir toda la información necesaria para la planificación de los trabajos, para facilitar el uso y la aplicación del mantenimiento.
Los objetivos de las órdenes de trabajo son:
- Solicitud del parte de trabajo y selección por operación del tipo de trabajo.
- Asignación del método adecuado y los trabajadores capacitados para la realización del trabajo.
- Minimizar el coste mediante el uso eficaz de los recursos.
- Mejorar la planificación y programación del mantenimiento.
- Mantener el control de calidad y la eficacia de las operaciones.
- Mejorar el mantenimiento con la retroalimentación de las órdenes de trabajo.
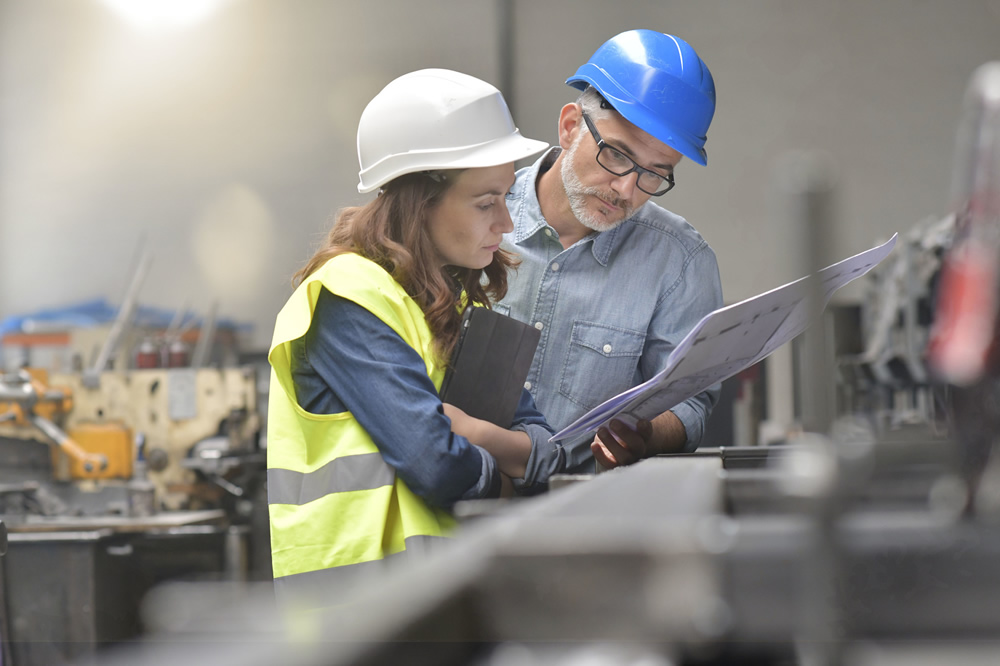
Uno de los temas fundamentales dentro del sistema productivo, como se ha comentado en temas anteriores, es el establecimiento de controles de mantenimiento con el objetivo de evitar pérdidas en el sistema.
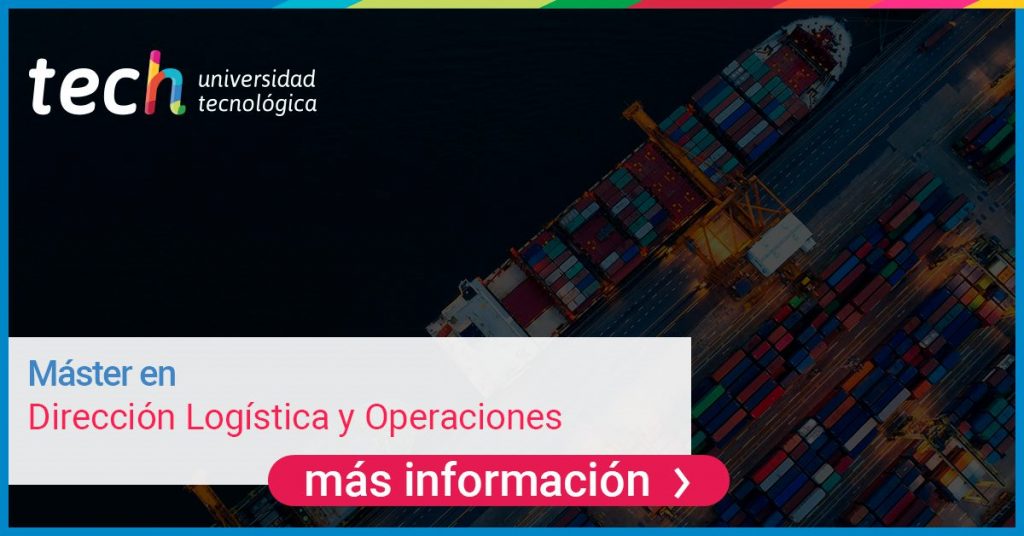
Si estás interesado en profundizar en este ámbito de los negocios no te pierdas nuestro Máster en Dirección Logística y Operaciones, que cuenta con el temario completo y actualizado que necesitas para avanzar profesionalmente. Lo mismo ocurre con el Máster en Dirección de Compras y Aprovisionamiento, de 1500 horas lectivas y equivalente a 60 créditos ECTS, o con el Máster en Tributación Internacional, Comercio Exterior y Aduanas, que responde a la demanda del mercado de profesionales especializados en este ámbito.