Warning: strpos() expects parameter 1 to be string, array given in /home/site/wwwroot/wp-content/themes/twentynineteen-child/functions.php on line 163
Un árbol de transmisión, también denominado “flecha”, es un elemento rotatorio, generalmente de sección circular, que se emplea para transmitir potencia, es decir, momento torsor, o torque, y velocidad angular, entre dos o más elementos, que incluyen engranajes, poleas, volantes de inercia, frenos, embragues, acoplamientos, rodamientos y cojinetes, etc. Por su parte, se denomina eje a un elemento no giratorio, que no trasmite potencia ni momento torsor y se utiliza para soportar poleas, ruedas rotatorias y elementos similares, es decir una viga estática. El diseño de árboles de transmisión resulta una tarea compleja, realizada en su mayoría por los profesionales en ingeniería mecánica.
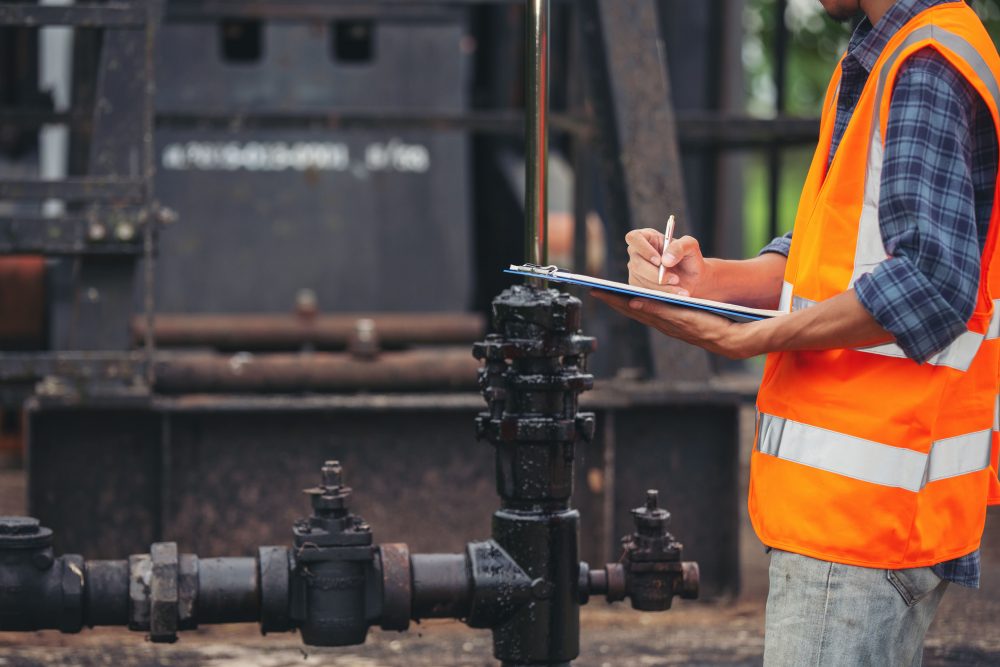
Árboles y ejes
Para el cálculo de árboles de transmisión y ejes se deben considerar los siguientes factores:
Selección del material
La rigidez de un árbol de transmisión obedece tanto al módulo elástico, o módulo de Young, del material como al momento de inercia de la sección. Generalmente, se utilizan aceros de bajo carbono, estirado en frío o laminado en caliente tipo ANSI 1020 -1050; que tienen módulos elásticos muy parecidos, aproximadamente 200 – 210 GPa; por lo que la diferencia de rigidez se da por el diámetro de la sección circular. Por último, se deben considerar las tolerancias de los diámetros, que normalmente se encuentran entre grado IT6 e IT11, y tener en cuenta que usar tolerancias demasiado estrictas supone un encarecimiento exponencial del coste de fabricación.
Configuración geométrica
La configuración de un árbol para acomodar los elementos de transmisión resulta fundamental para analizar esfuerzos, de esta configuración depende el valor de los momentos flectores y de los esfuerzos de pandeo. De modo general, se debe reducir la longitud de los árboles y evitar los voladizos procurando que todos los elementos queden situados entre los apoyos, para reducir los momentos flectores.
También es importante tratar de limitar el número de rodamientos a 2, para que el sistema sea estático y se eviten tanto los momentos flectores como el exceso de rigidez que generan los sistemas hiperestá ticos; sin embargo, hay veces que esto no es posible porque se debe limitar la deformación máxima. Por último, se debe considerar la facilidad del montaje y desmontaje de los elementos acoplados al árbol.
Esfuerzo y resistencia
Los esfuerzos dominantes en un árbol de transmisión son los de torsión (τ) y flexión (σ), aunque de modo secundario se pueden encontrar esfuerzos de pandeo (σ), cortadura (τ) y el derivado de los ajustes forzados (σ). Se debe considerar el efecto de la concentración de esfuerzos, que se encontrará en los sucesivos cambios de sección del árbol, por lo que resulta interesante aplicar técnicas que la reduzcan. El cálculo de resistencia se realiza con base en la siguiente secuencia:
- Se calcula la media y la amplitud de los momentos flectores y torsores.
- Se calcula la media y la amplitud de los esfuerzos axiales (σ) y de cortadura (τ) considerando la concentración de tensiones.
- Calcula la suma de las medias y la suma de las amplitudes, utilizando un método como el de Von Mises.
- Se calcula el coeficiente de seguridad n según un criterio reconocido de fatiga de esfuerzos fluctuantes.
Un método alternativo y simplificado de cálculo es el Código de Calderas y Recipientes a Presión ASME, que permite obtener el coeficiente de seguridad n con base en los momentos torsores y flectores máximos, y otros que se calculan en función de la forma de aplicación de las cargas.
Deformación y rigidez
Es importante comprobar las deformaciones máximas, tanto las producidas por esfuerzos de flexión como por los de torsión. Las principales son:
- Deflexión, producida por flexión o por esfuerzo cortante, especialmente en los puntos en los que se colocan los engranajes
- Deformación por torsión
- Ángulo de la pendiente de flexión, especialmente en los apoyos
A estas deformaciones se les debe añadir las producidas por los ajustes de elementos como rodamientos en el árbol de transmisión.
Frecuencias naturales y fenómenos de resonancia
Cualquier árbol de transmisión con masa tiene una frecuencia natural, también denominada “velocidad crítica”, que depende de su configuración, de la rigidez, es decir del momento de inercia, su módulo elástico, y su masa, lo que son sus dimensiones y su densidad. Por lo que se puede resumir que la velocidad crítica ω1 depende de su forma y del material con el que se ha construido.
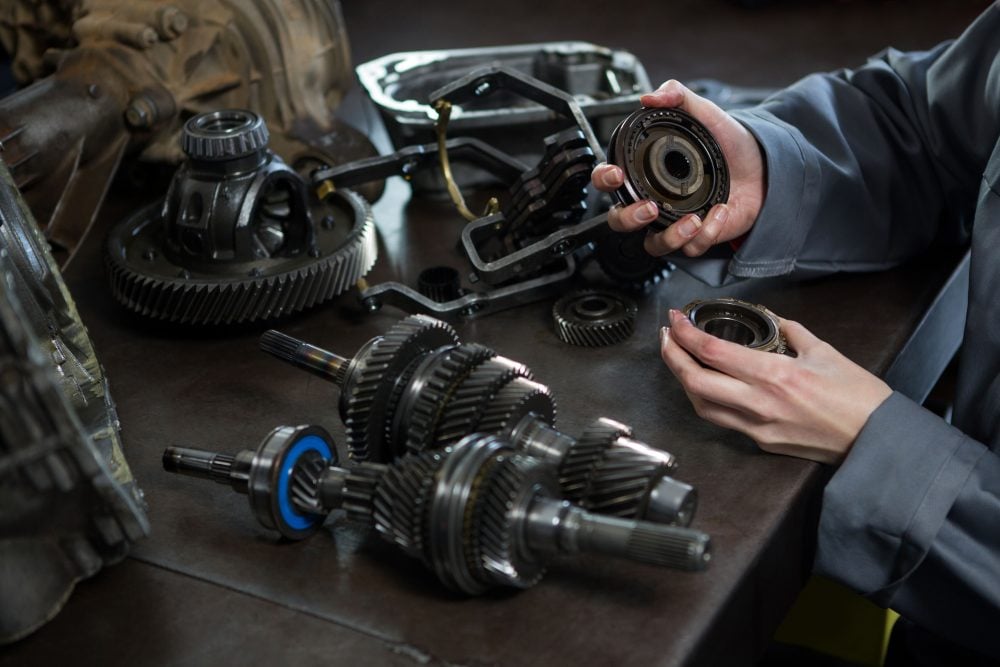
Cuando un árbol de transmisión gira se genera una deformación producida por la fuerza centrífuga resultada de una vibración, si la frecuencia de esta vibración, o las de otras que se aplican al árbol, coincide con la frecuencia natural del árbol, se obtiene un fenómeno de resonancia que aumenta la deformación hasta generar el fallo. Para evitar problemas, la frecuencia natural del árbol debe ser 2 o 3 veces superior a la velocidad angular máxima.
Chavetas y árboles estriados
Para fijar elementos rotatorios, como engranajes o poleas, al árbol de transmisión y transmitir potencia se utilizan diferentes componentes, como chavetas, pasadores, tornillos de fijación, anillos de retención, ejes estriados y zunchos.
Chavetas
Transmiten momento torsor, pero no soportan cargas axiales. Se calculan a cortadura y a aplastamiento, con coeficiente de seguridad algo más bajo que el resto de los componentes, de manera que sirvan de fusible. Su ancho y alto está normalizado, por lo que solo se debe calcular la longitud de la chaveta. Existen chavetas cuadradas, de cuña y chavetas Woodruff o de disco, con forma semicircular, que son sencillas de instalar y siempre se colocan en la posición exacta. La fórmula general es la siguiente, en esta w es el ancho, h la altura y L la longitud de la chaveta. Cuando se utilizan 2 o más chavetas se aplica un factor de simultaneidad de entre 0,7 y 0,8.
Pasadores
Se utilizan para posicionar axialmente el elemento y transferir momento torsor, soportan pequeñas cargas axiales. Sus dimensiones también están normalizadas.
Tornillos de fijación
Se utilizan para soportar esfuerzos axiales, se basan en el par de apriete para evitar sufrir esfuerzos de cortadura.
Anillos de retención
Se utilizan para fijar axialmente los elementos del árbol de transmisión. Se debe tener en cuenta la concentración de tensiones generada y no se deben instalar en puntos con momentos flectores elevados.
Ejes estriados
Consisten en tallar estrías directamente en el árbol, tiene el efecto de múltiples chavetas. Las ranuras pueden ser rectas o tener forma de evolvente, estas últimas son más fáciles de fabricar y permiten transmitir mayores momentos torsores.
Zunchado
No es un componente, consiste en unir un elemento al árbol mediante interferencia. Las interferencias más habituales son los ajustes H7/p6 para asegurar rigidez y alineación, H7/s6 para soportar momentos torsores medios, y H7/u6 para soportar momentos torsores mayores. Se debe tener en cuenta que estas interferencias producen esfuerzos de tipo axial en dirección axial y en dirección radial.
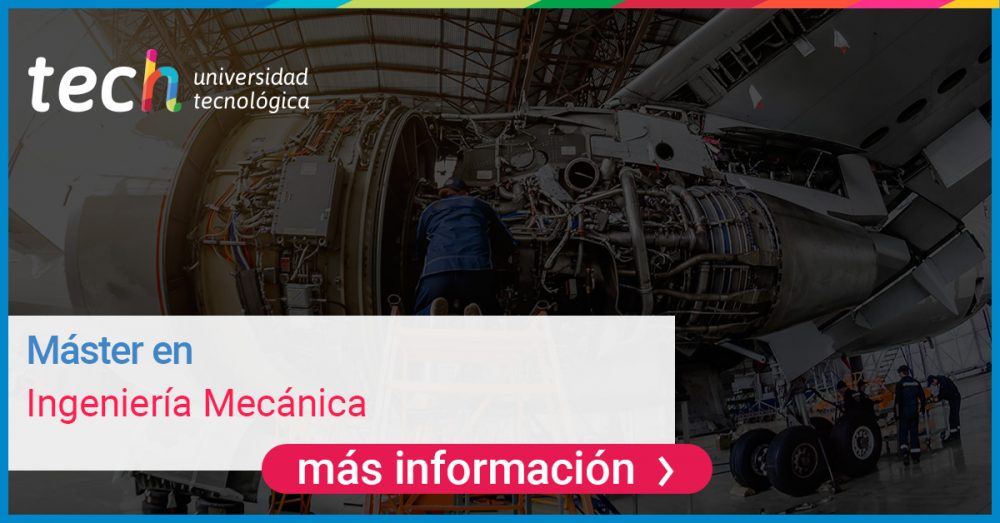
Diseño de componentes desde la ingeniería
El profesional en ingeniería tiene la habilidad de crear diferentes mecanismos y estructuras dependiendo de su área de aplicación. Dentro de las múltiples tareas que desarrolla, el diseño y cálculo de la creación y fabricación de estos componentes resulta una tarea compleja que requiere de experiencia y conocimiento. La educación del ingeniero juega un papel básico acá, ya que este es el punto de partida para un correcto desarrollo de esta labor.
TECH Universidad Tecnológica se posiciona actualmente como la mayor Universidad virtual del mundo. Gracias a su novedosa metodología digital cada uno de los profesionales de su alumnado cuenta con amplias habilidades para el desarrollo de sus labores. Caso ejemplo es su Facultad de Ingeniería, donde se desarrollan posgrados tales como el Máster en Industria 4.0 y Transformación Digital y el Máster en Dirección de Administración Industrial. Sin embargo, para aquellos profesionales que buscan dominar el área del diseño mecánico, no cabe duda que su decisión se debería inclinar por el Máster en Ingeniería Mecánica.